How to Reduce Downtime of Supply Chain Automation
In today’s high-speed economic environment, the ability to reduce downtime in supply chain automation systems is pivotal for sustaining business momentum and competitive advantage. As global markets evolve and consumer demands increase, the reliability of these automated systems directly impacts the ability to deliver products and services efficiently and effectively.
Unplanned downtime in these systems can quickly lead to significant operational disruptions, such as delays in production, missed delivery targets, and substantial financial losses that can erode profit margins and damage brand reputation.
With the integration of advanced technologies and systems, supply chain automation has reached new heights of complexity and efficiency. However, this advancement also brings challenges, particularly in maintaining continuous operation without interruptions. Addressing these challenges requires a strategic approach that not only addresses problems as they occur but also anticipates and prevents them before they can negatively impact the business.
Moreover, as industries continually push for higher productivity and lower operational costs, the pressure on supply chain automation systems to perform flawlessly under tight schedules is immense. In this context, maximizing uptime and reducing downtime is not merely beneficial; it becomes an essential cornerstone of operational strategy.
The High Cost of Unplanned Downtime
Unplanned downtime is a pervasive issue that can cost companies millions, as seen in various sectors. For instance, a downtime incident in the automotive sector can escalate to losses exceeding $2 million per hour, showcasing the high stakes involved.
The “True Cost of Downtime 2022” report by Siemens indicates that Fortune Global 500 companies face an average downtime cost of $129 million per facility annually, a staggering 65% increase from previous years. David Sandiland, thanks to his experience at Igus Motion Plastics, notes that he had spoken with facility managers during his career who estimated the cost of downtime at a staggering $10,000 a minute.
The Domino Effect of Downtime
One compelling account shared by Jay Blinderman, SVP of Go-to-Market at SVT Robotics, underscores the dramatic impact of downtime on a manufacturing operation.
Jay recounts a scenario from a previous role involving a European chocolate manufacturing facility that relied heavily on a sophisticated enterprise software package to orchestrate its operations. The system was integral to everything from production schedules to the final boxing of products for shipment. Particularly critical was its role in managing the flow of raw materials, such as chocolate, to the production lines.
In this facility, the precision of system timing was crucial. A disruption of just a few minutes could cascade into significantly larger issues. Jay explained, “In their case, if the line was shut down for 9 minutes or less, they could start back up again with very little disruption. But once it reached the 10-minute mark, they then had to shut the line down for an hour or more, possibly even the entire day.”
They either had to solve the problem in 9 minutes or less, which cost around $10,000, or it became a $100,000 or larger problem after the 10-minute mark.
Jay Blinderman, SVP of Go-to-Market, SVT Robotics
This drastic action was necessary because any stoppage of 9 minutes or longer required a complete system flush. “They had to lose all the chocolate that was on the line and then sanitize all the lines,” Jay added. This not only resulted in direct material losses but also triggered a costly and labor-intensive recovery process.
The financial implications of such downtime were significant. “They either had to solve the problem in 9 minutes or less, which cost around $10,000, or it became a $100,000 or larger problem after the 10-minute mark,” Jay noted. This example illustrates not just the direct costs associated with lost materials and production time but also the broader financial impact due to delayed deliveries.
Moreover, a single system failure has a domino effect. It often leads to missed customer delivery deadlines, compounding the financial repercussions. “Once they’ve missed their deadlines, that snowball starts to roll. Because then they’re missing customer delivery deadlines and there’s the cost of that delay,” Jay explained. For instance, penalties from major retailers for late deliveries can add substantial costs, further impacting the company’s bottom line and customer relationships.
Practical Strategies To Reduce Downtime
Maximizing uptime is critical to maintain efficiency and prevent costly disruptions in supply chain operations. Here are some practical strategies to consider when trying to maximize the uptime of supply chain automation:
Real-time Monitoring
Real-time monitoring systems equipped with user-friendly interfaces enable immediate access to critical operational metrics. These systems are designed to not only display data but also analyze it in real time, providing actionable insights. Here are some ways to empower real-time monitoring to maximize uptime:
- Intuitive Dashboards: Developing dashboards that provide at-a-glance views of system health, performance metrics, and alerts. These interfaces should be customizable to cater to the specific needs of different users, from floor managers to executive leadership.
- Integration with Mobile Devices: Enabling real-time alerts and monitoring on mobile devices ensures that key personnel can stay informed and reduce downtime by reacting quickly to potential issues, regardless of time or location.
Troubleshooting Capabilities
Strengthening the troubleshooting capabilities of Tier 1 support personnel is vital for reducing response times and enhancing system uptime. Training these front-line responders to perform initial diagnostics can drastically speed up the resolution process when combating downtime.
- Comprehensive Training: Equip Tier 1 support with detailed training on common issues and troubleshooting procedures. This training should include simulations and real-world scenario practices to build confidence and efficiency.
- Enhanced Diagnostic Tools: Provide advanced diagnostic tools that can guide the support personnel through a step-by-step troubleshooting process, making it easier to identify and address issues quickly.
Proactive Monitoring and Degradation Detection
Moving beyond mere reactive monitoring to a more proactive approach can transform how downtime is managed. Constant monitoring to detect early signs of degradation in system performance is crucial for preventing future downtime incidents. Here are some key focus areas to consider:
- Predictive Alerting: Implement systems that track real-time performance and use predictive analytics to forecast potential failures before they occur in order to greatly reduce downtime. These alerts can notify teams of the likelihood of a problem before any symptoms are detectable.
- Active Degradation Monitoring: Continuously monitor the health of systems to identify any signs of degradation over time. This ongoing vigilance helps to catch and address wear and tear before it leads to failure, effectively preventing costly downtime.
- Continuous Feedback Loops: Establish continuous feedback loops where real-time data is constantly analyzed to refine predictive models and alert parameters. This dynamic adjustment helps keep the systems in tune with the actual operational conditions and peculiarities of the supply chain processes.
By integrating these advanced strategies into their operational frameworks, companies can significantly improve uptime for their supply chain automation systems. Data transparency fosters a culture of informed decision-making, while real-time monitoring and enhanced troubleshooting capabilities ensure issues are addressed promptly and efficiently.
Proactive monitoring and active degradation detection further safeguards operations, supporting sustained productivity and business growth. This comprehensive approach not only prevents disruptions but also enhances supply chain resiliency.
Data Transparency
Data transparency in supply chain automation involves making operational data accessible and understandable across different levels of the organization. This openness allows for more informed decision-making and better collaboration between departments. Here are some ways to improve data transparency to maximize uptime:
- Centralized Data Access: Utilizing a centralized platform where all performance data is collected and visible helps identify trends and potential issues across the entire supply chain. This approach ensures that decisions are based on the full context of operational data, leading to more effective resource management.
- Cross-functional Teams: Encouraging cross-departmental teams to engage with this data fosters a deeper understanding of how different areas of operation impact each other, leading to more proactive and holistic strategies to prevent downtime.
How the SOFTBOT® Platform Maximizes Uptime
In the rapidly evolving landscape of supply chain automation, maintaining operational uptime is more critical than ever. Even brief downtime can result in substantial financial losses and operational disruptions. SVT Robotics’ SOFTBOT Platform addresses these challenges head-on by enhancing the integration, monitoring, and management of automation systems. Here’s a detailed look at how the SOFTBOT Platform can reduce downtime with faster discovery, triage, and resolution.
What makes the SOFTBOT Platform different?
Seamless Integration: One of the key differentiators of the SOFTBOT Platform is its ability to integrate seamlessly with existing systems without modifying underlying technologies or APIs. Unlike traditional integration approaches that often require extensive custom code, the SOFTBOT Platform offers tech-agnostic, prebuilt connectors that integrations host systems to leading technology providers. This capability not only simplifies the integration process but also reduces the risks associated with modifying critical operational systems.
Real-Time Monitoring: The SOFTBOT Platform excels in providing comprehensive real-time monitoring capabilities. This feature is crucial for IT and operations teams to have visibility into all aspects of the supply chain automation processes. With real-time data at their fingertips, these teams can quickly identify and address potential issues before they escalate into costly downtime.
Data Standardization and Transparency: The platform aggregates and standardizes data across various systems, enhancing data transparency. This standardization allows businesses to make informed decisions quickly, leveraging accurate and consistent information across different segments of their operations.
Key Features That Maximize Uptime
Proactive Alerting System: The platform’s alerting capabilities are designed to notify teams immediately when potential issues are detected. This proactive approach ensures that issues can be addressed promptly, often before they affect the system’s operations, thereby minimizing downtime and its associated costs.
Scalability and Flexibility: The platform’s flexible nature allows it to adapt to various technologies and systems, from multiple warehouse management systems (WMS) to advanced robotics. This adaptability is crucial for businesses looking to scale operations or integrate new technologies without extensive downtime for system overhauls.
Self-Documenting and Easy to Modify: All SOFTBOT Connectors are self-documenting, simplifying maintenance and updates. This feature is particularly beneficial for IT teams as it allows for easier troubleshooting and faster modifications when needed, reducing downtime during upgrades or system changes.
Benefits of the SOFTBOT Platform for IT Teams
Reduced Dependency on Custom Code: Using the SOFTBOT Platform significantly lowers the costs and complexities of maintaining traditional custom integrations by minimizing the need for bespoke code. IT teams can manage and monitor systems more efficiently without being bogged down by the intricacies of custom-coded solutions.
Enhanced Operational Visibility: The SOFTBOT Platform’s single-dashboard view gives IT teams comprehensive visibility into system operations. This visibility is crucial for monitoring system health, performing diagnostics, and making data-driven decisions to reduce or even prevent downtime.
Streamlined Issue Resolution: The platform’s ability to quickly pinpoint issues and provide actionable insights helps IT teams resolve problems faster. This efficiency not only maximizes uptime but also enhances the overall productivity of the teams involved.
Cost-Effectiveness: The SOFTBOT Platform offers significant cost savings by reducing the time and resources needed for system maintenance and issue resolution. These savings can be redirected toward other strategic initiatives within the organization.
Using the SOFTBOT Platform to Reduce Downtime
As businesses increasingly rely on automation to streamline supply chain processes and improve efficiencies, the impact of downtime becomes more pronounced, emphasizing the need for robust solutions like the SOFTBOT Platform. This platform by SVT Robotics not only minimizes the risk of costly interruptions but also provides a comprehensive suite of tools designed to enhance system integration and real-time operational oversight.
The SOFTBOT Platform’s unique approach to managing automation systems—free from the constraints of traditional custom coding and inflexible integrations—empowers IT teams with unprecedented control and visibility. This ensures that operations remain fluid, deadlines are met, and financial losses are curtailed, ultimately fostering a more dynamic and competitive business environment. In an era where operational agility and reliability are paramount, the SOFTBOT Platform stands out as an essential toolset for maximizing uptime and driving supply chain success.
Global 3PL Case Study
Replacing Existing Integrations to Maximize Uptime and Innovation
Learn why the SOFTBOT® Platform was selected by this global 3PL to replace existing, working integrations. This case study features multi-point integrations with Manhattan, Blue Yonder, Addverb, Locus Robotics and Packsize and 6 River Systems, Part of Ocado Group.
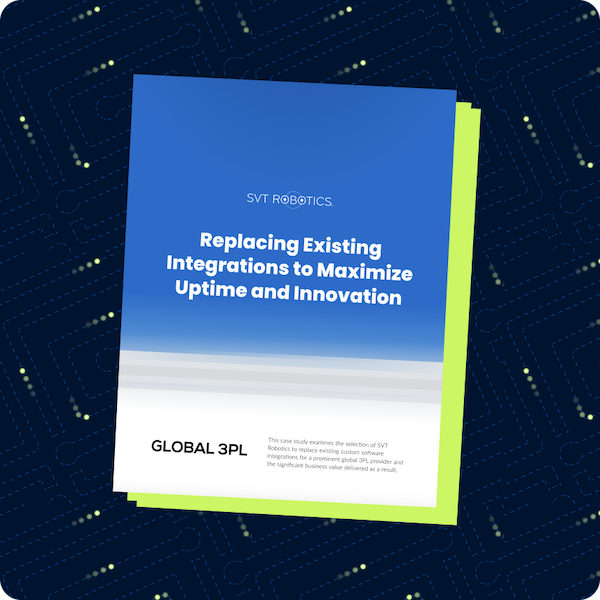
Barrett Distributions Centers Case Study
Deploying CMC Packaging Automation Before Cyber Five
This 3PL wanted to introduce packaging automation from CMC in order to optimize their operations, yet needed the new technology integrated quickly. Learn how they deployed ahead of Cyber Five/peak season and laid the groundwork for future innovations by using the SOFTBOT® Platform.
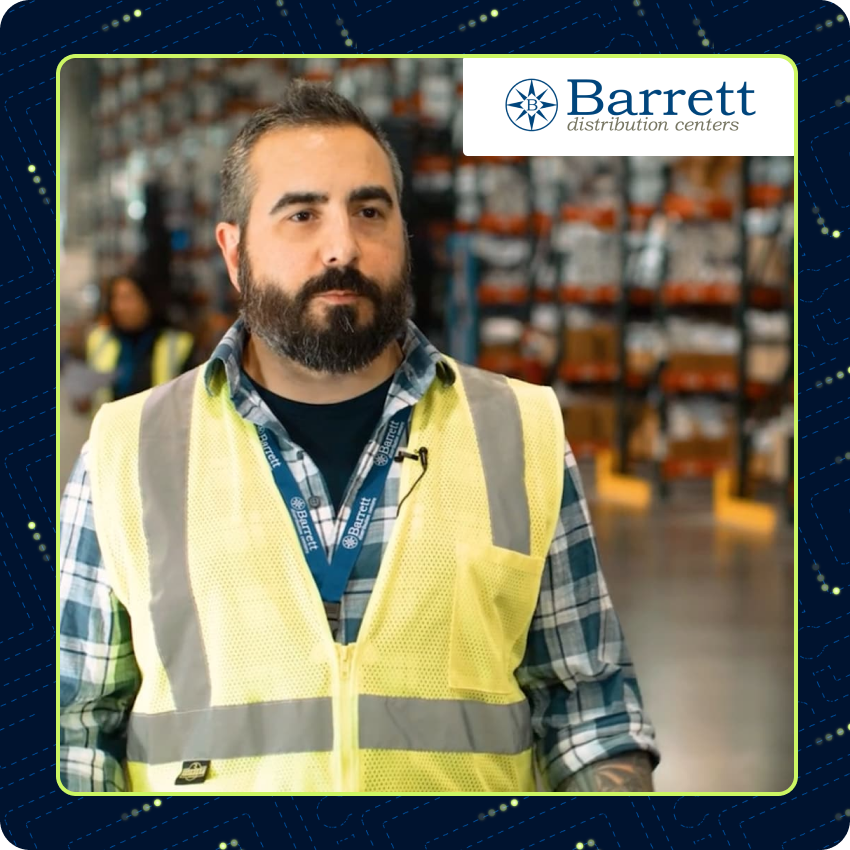